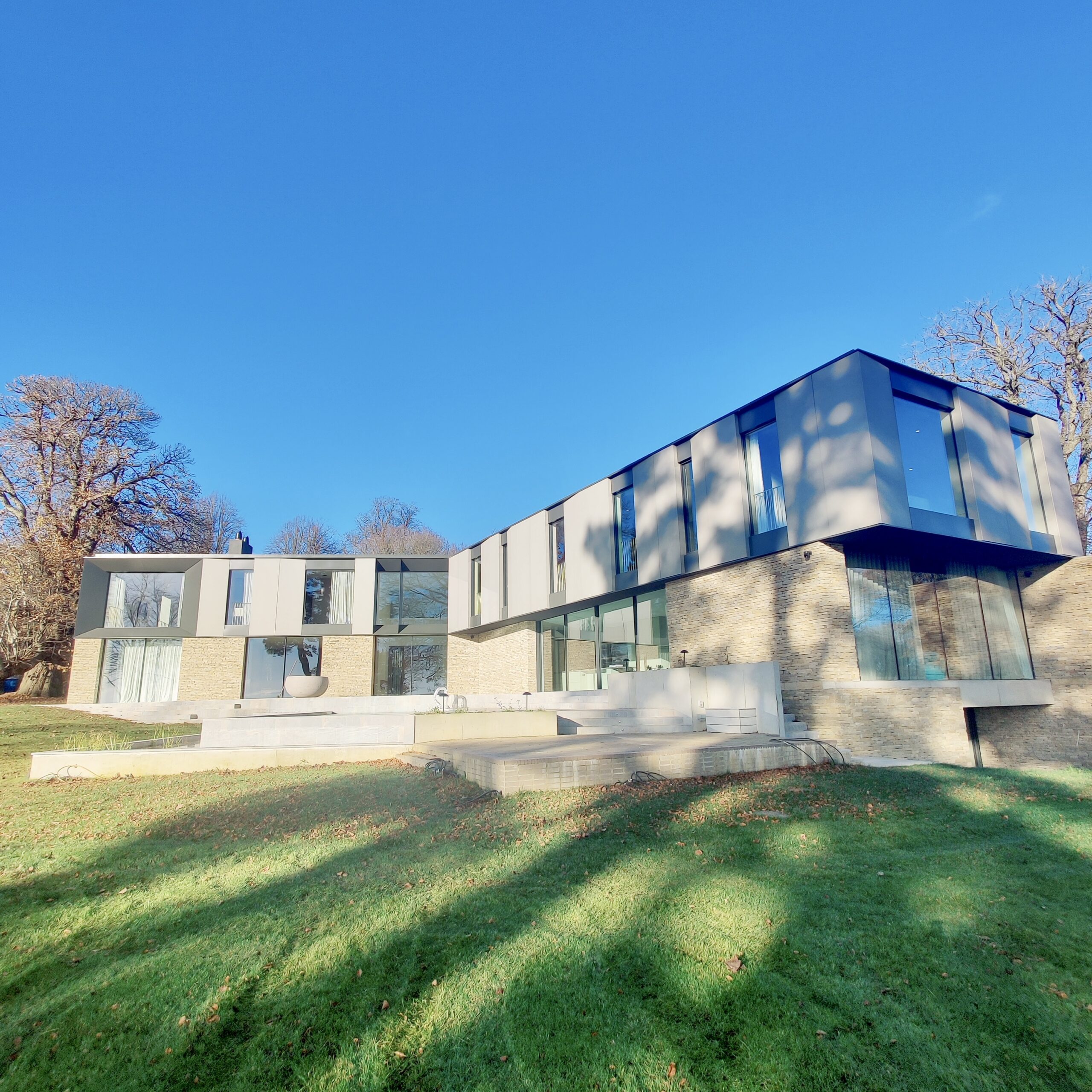
The second new-build home within the grounds of a Grade II listed estate in Oxfordshire.
Location
Sector
Client
Private
Architect
deDraft
Budget
Undisclosed
Status
Due for completion 2023
Images
DeDraft
SD Team
Download PDF
Project tags
AYN3 is a three-storey house set out in a Y shape. A large spanning steel frame removes the need for internal columns, achieves beautiful cantilevers and overhangs, and allows for large uninterrupted views through the glazing across the listed 24 acre estate.
The steel frame has a concrete and metal deck floor placed within the depth of the beams to create a shallow structural floor zone and minimise internal floor heights. The framing solution was also selected as it is robust, has excellent acoustic and vibration qualities and was fast to construct on-site.
Careful detailing by our team ensures a high quality finish to the exposed insitu reinforced concrete clad elements which provides durability, avoids thermal bridging issues, and also achieves the architectural aesthetic requirements.
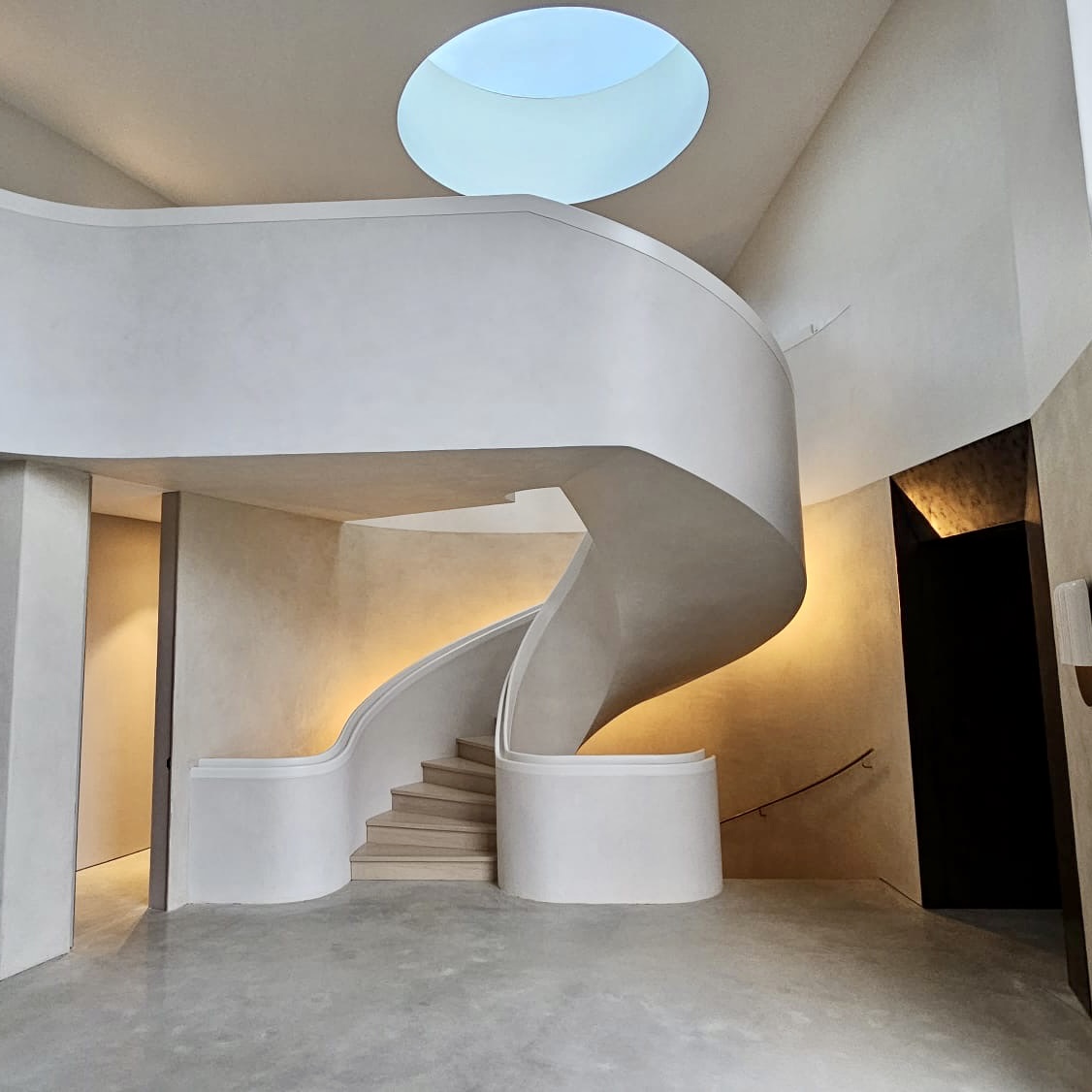
A basement beneath the full footprint of the building caters for an impressive car collection with integrated car turntable, gym space, a sprung dance floor studio, spa complex with steam room and sauna, and a simulator room housing a car simulator constructed from a real historic racing car!
We provided the temporary works design services for the construction of the basement and for the design of the crane base required by the contractor.
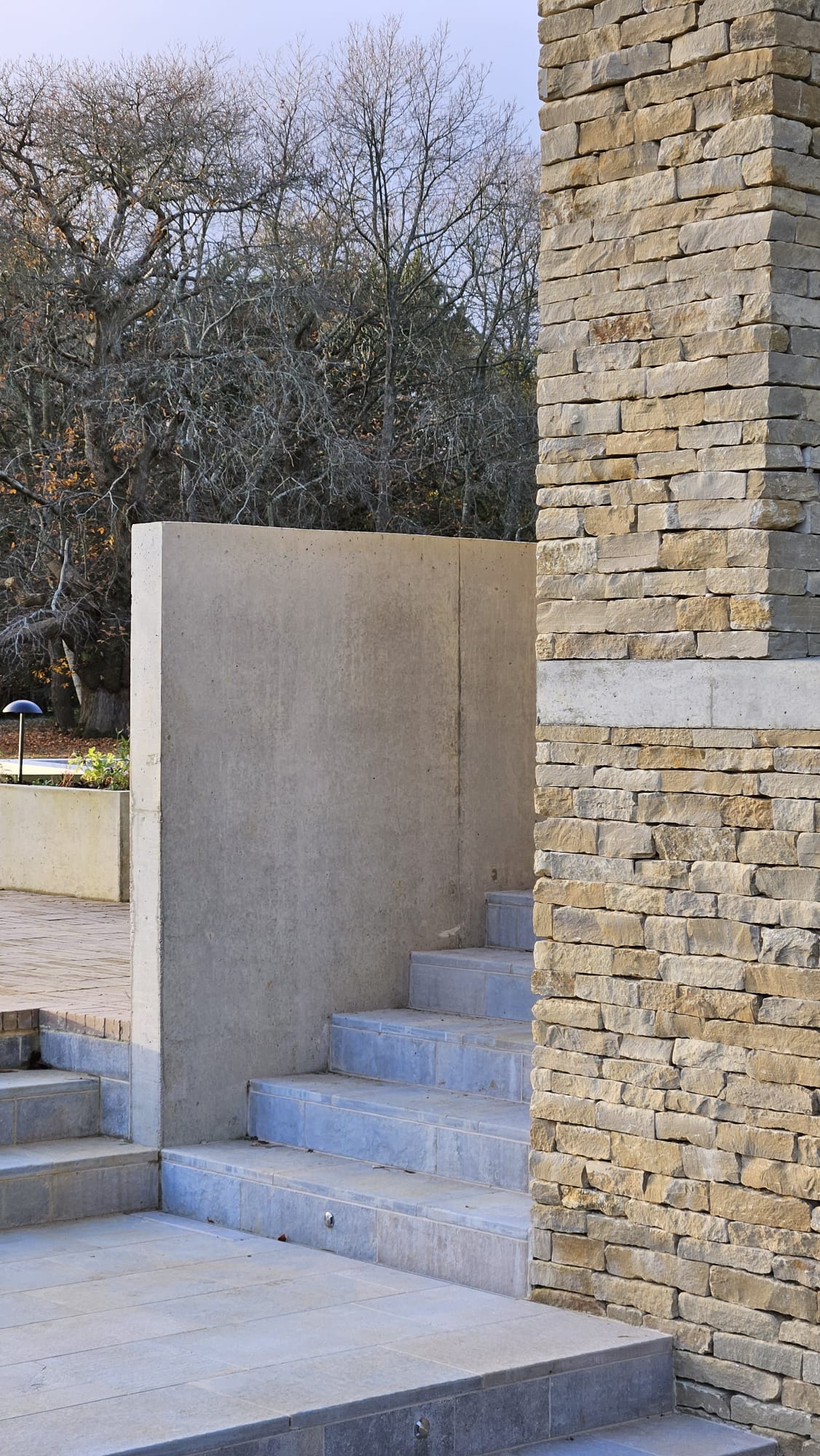
The 6m tall freestanding dry stone walls extend out from the building to provide architectural articulation and privacy. These were carefully engineered with integrated steel wind posts cantilevered from the hidden reinforced concrete retaining wall below. Prefabricated meshed reinforcement sheets were used to accelerate the basement programme and we worked closely with the specialist waterproofing contractor to ensure a robust and watertight structure.
A central design feature is a stunning double height atrium with floating spiral staircase and cantilevered column-free landing.
We collaborated with the contractor and precast stair manufacturer on the design of the precast stair which was fabricated within the factory and craned into place on site. The stair and cantilevered landing connection forms a key part of the performance of the stair. To meet vibration performance requirements the cantilevered steel landing beams each have 35mm thick steel flanges and weigh over a tonne each!
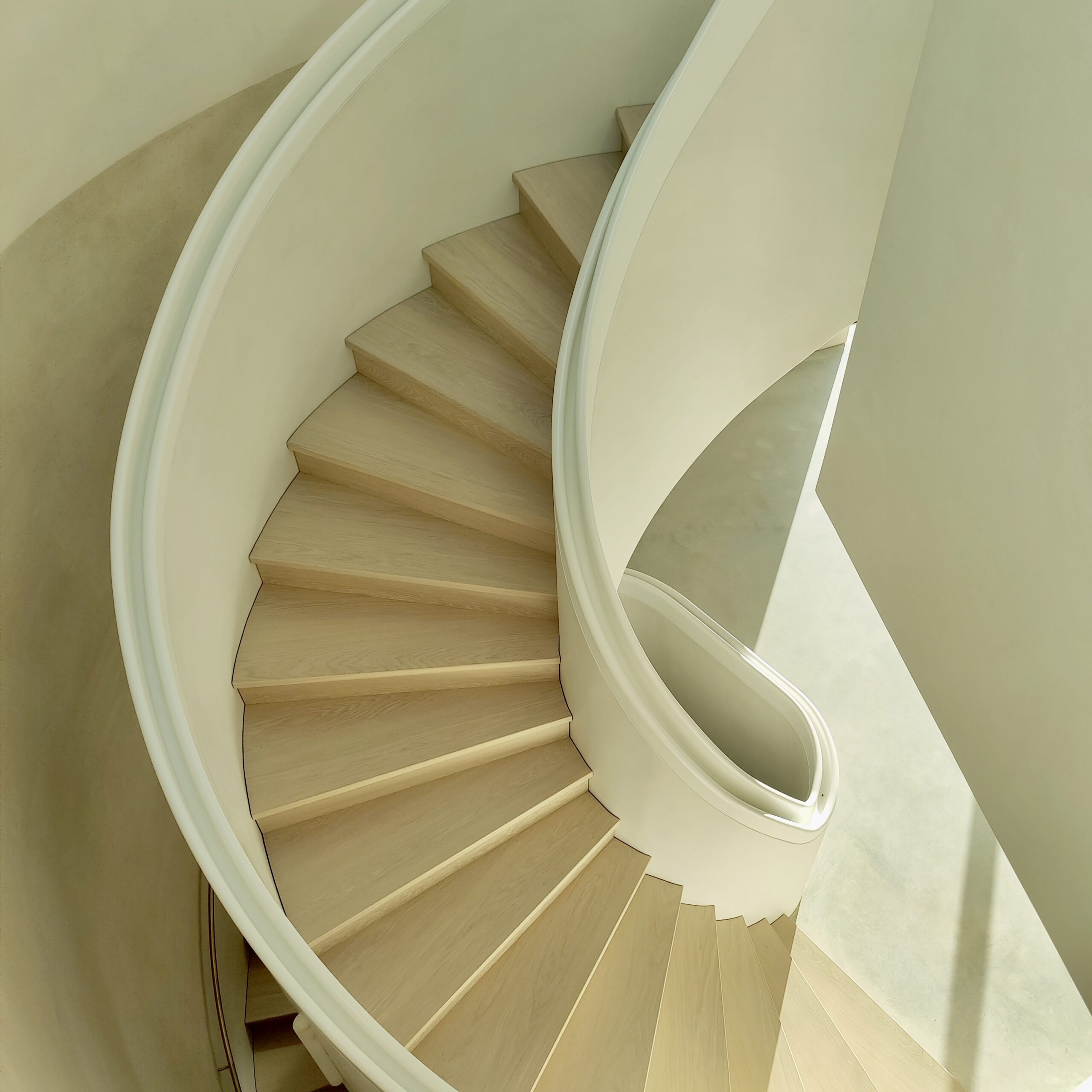
All concrete and steel elements were designed by us using advanced 3D analysis software to maximise the efficiency of the structure and minimise material use within the constraints of the ambitious design parameters. The house uses ground source heat pumps, a Mechanical Ventilation with Heat Recovery (MVHR) system, and photovoltaic cells across the roof to lower its operational carbon footprint.
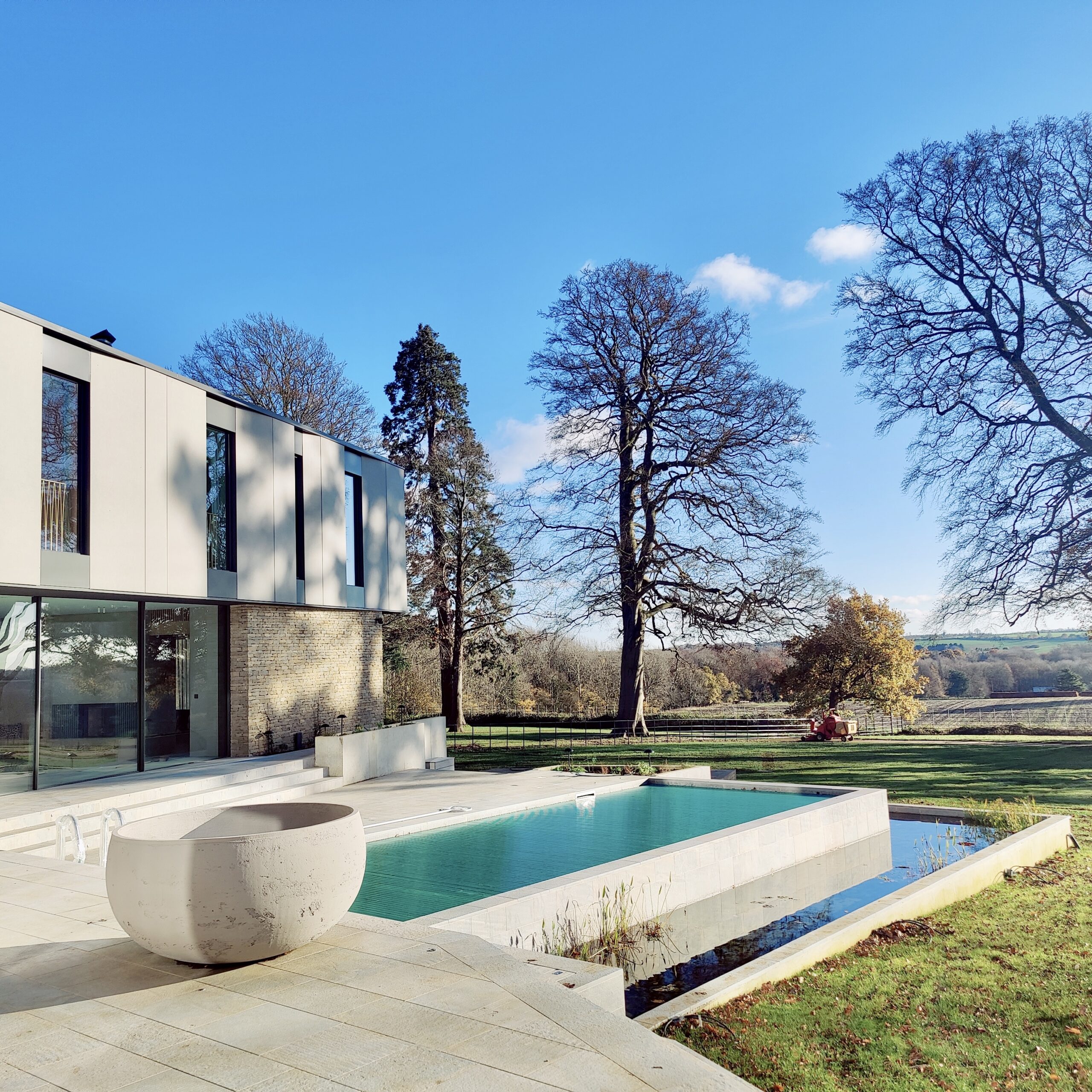
There are many protected and ancient trees located within close proximity to both homes and so coordination with arboriculturists and landscape architects was paramount, particularly with regards to our SuDS and soakaway drainage design.