Working in the intersection between technology and social science/high quality of urban life, PLP Architecture is undoubtedly one of the driving forces when it comes to innovation and sustainability in architecture.
SD Director Mike Davies met with PLP Architecture Partner, Mark Kelly, to discuss the challenges our industry is facing to get to Net Zero, how new technologies can help deliver added value to clients, and the limits and potentials of timber in construction.
Mike Davies – SD Engineers
What would you say are the biggest challenges you see in the industry for getting to Net Zero?
Mark Kelly – PLP Architecture
I think the industry as a whole is rising to the challenge and are working hard to hit RIBA 2030 requirements, but there is no doubt that there is still a lot to do given where we are at.
MD – SD
Especially when we’re still relying on legislation to come through in this country…
MK – PLP
Some clients and funds, and some people are really interested in cutting carbon emissions and want to do the right thing. However, there are still big players, especially for large-scale commercial developments, who are still trying to understand the implications. I remember the wave of practices signing up to the Architects Declare campaign at the beginning. It’s important to keep the momentum going, but commercial viability is still a major drive for clients and developers.
MD – SD
I think as designers we can play a role advising our clients.
MK – PLP
Yes, and we need legislation. We can spend a lot of time educating our clients but it’s their decision at the end of the day. I’ll be talking to clients, going through sustainable options and having difficult conversations trying to inform their decisions, and I’ll be wondering if other architects are saying the same things.
MD – SD
You have undertaken detailed carbon counting assessments on your schemes recently. What would you say the biggest thing you’ve learned from reviewing carbon data is?
MK – PLP
I think there is a lot of potential there. We collect and review carbon data on our projects but sometimes the design decisions are led by other factors… Legislation would make that design decision-making process more effective.
MD – SD
It’s about finding the middle ground, isn’t it? Finding the balance between generic, formulaic design and a unique aesthetic form of expression in architectural design. Taking that data to understand the effect these decisions will make on embodied carbon and giving something back in return.
MK – PLP
Our work with CLT like the Oakwood Tower with Cambridge University produced incredible publicity, and sometimes there is a clear sustainability drive for a scheme, like the timber-frame building we did in Corso Como, Milan. But then we were working on this project in The Netherlands which was going to have a concrete core with timber framing around it… To be honest, I am not completely convinced that CLT is the way forward. I think concrete might be, due to its longevity and the potential of reusing it in the future. I think a combination of the two may be actually where the industry ends up going.
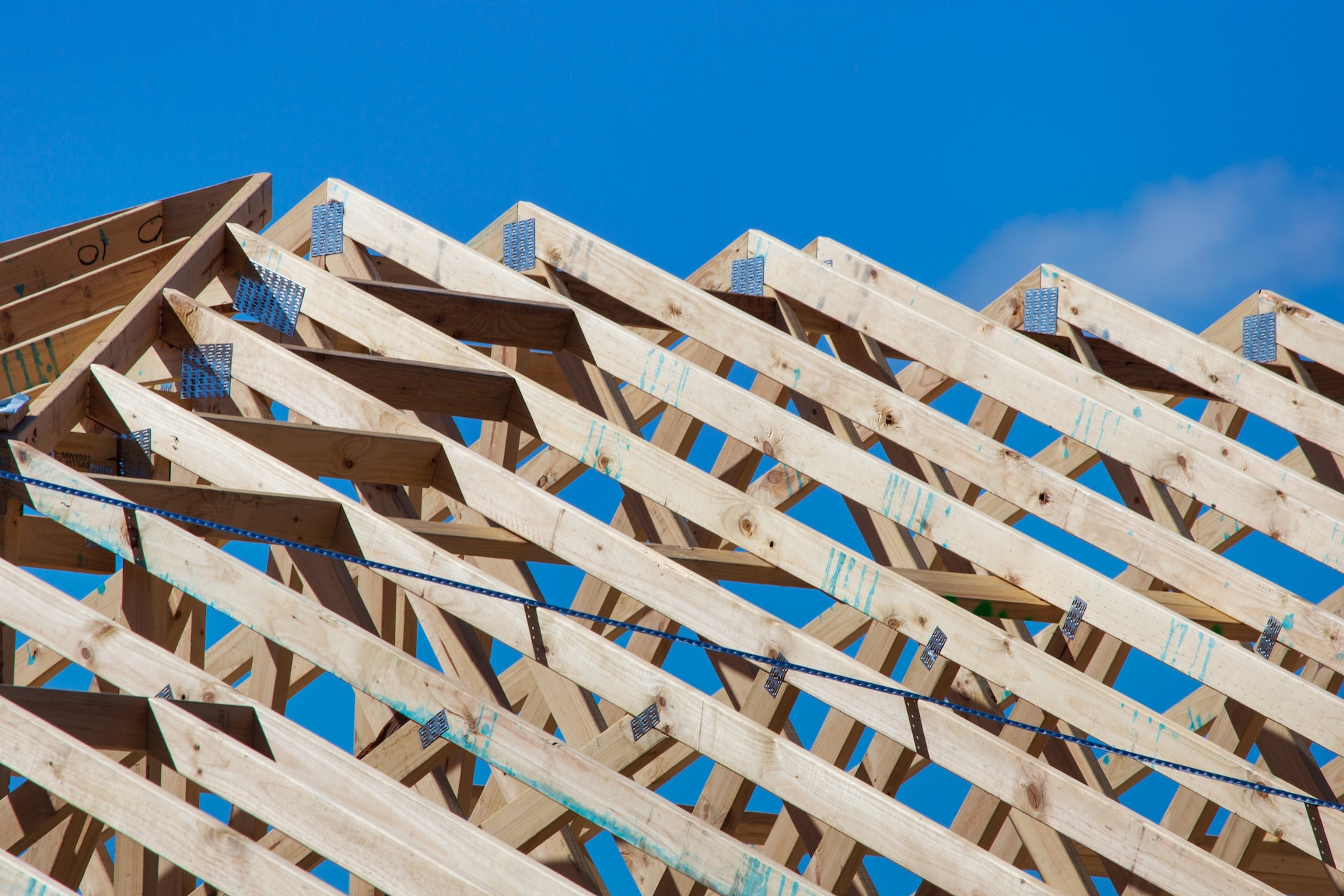
MD – SD
So what was it that killed the CLT scheme and it went back to concrete as the determining factor? Cost?
MK – PLP
Cost. But specifically for the UK, I think the insurance industry is a little behind and makes clients very wary when it comes to using timber. I also think that detailing becomes critical for timber buildings which adds a level of complexity to its use in construction.
MD – SD
Another downside of timber is that we haven’t got enough sustainable timber in the UK for it to be the only answer.
MK – PLP
We do have to import it and, although supply might not necessarily be an issue, I would imagine a client would be nervous to use it when other buildings are being ripped apart because they’ve got damp timber.
MD – SD
It seems there is a skills shortage in the UK mass timber industry, both in effective detailing and in construction.
MK – PLP
Yes, I think so. There are some Scandinavian countries that have a strong sector and are quite advanced in its use and are addressing some of these issues. I am sure we will get better at it, but at the moment I am not sure CLT is the key factor that will get us where we need to be to reach Net Zero.
MD – SD
PLP is a tech-focused business. What are you most excited about in terms of new technology coming through in the industry?
MK – PLP
We’ve got a lot of conversations happening about AI at the moment, and how we can use it to optimise our processes. I’d like to think that we’re a creative industry, and to be a creative company, you need to embrace technology. At PLP, we will look to use any sorts of technology available if that can help us push us in the right direction.
MD – SD
And give you a competitive advantage…
MK – PLP
I don’t think clients even understand the full potential of technologies like AI or VR! We don’t understand the full potential of it, and I think it will be a learning experience for all of us.
MD – SD
With recession and current market conditions which areas of the construction industry have the most potential for growth?
MK – PLP
We are looking at Life Sciences. It’s a small industry and very competitive which I think will unfortunately drive fees down here in the UK.
MD – SD
So your answer is to look overseas.
MK – PLP
I think we’re lucky to have an overseas profile.
MD – SD
What do you think some of the key benefits are in bringing in Architects and Engineers early in a project.
MK – PLP
There is definitely value in getting involved early on.
We’ll get approached by some clients, often overseas investors in the UK market, who have recently bought a building stock and wish to do a feasibility study. That asset might change ownership over time, and we often get asked to work on multiple schemes for the same asset.
Another example is Cleveland Clinic in London. We worked on the building before it even was a hospital. It was originally owned by W.R. Berkley, for whom we did some work, and then it was sold to Perella who eventually sold the lease to Cleveland Clinic. They, then, decided to hire us because we were familiar with the site and we’d happened to draw out possible hospital scenarios for that site.
It’s amazing how doing little bits of feasibility studies here and there can suddenly lead to very large commissions!
MD – SD
You have been at the company for a long time and seen it grow significantly. Andy and I started SD seven years ago and there’s now 25 of us. What advice would you give us if we were thinking of scaling up further?
MK – PLP
I joined KPF in 1994 and I think I was employee number 25 in London. I remained at KPF until PLP was formed in 2009. At PLP we started off with six people and six weeks later, we had a 60-person team strong.
I think we were very lucky because we had an international reputation already in 2009. Whilst clients transferred their projects to PLP, we only had a few projects that were actually paying decent fees. On the back of those projects, we were able to finance and do some work for people that we know over here. My advice would be to build a really good client base and treat those clients well. It is critical because you want clients who are going to come back to you. And the other thing is to grow on the back of projects. Don’t just expand for expansion sake.